Digital Solutions | Industry 4.0
Industry 4.0 refers to the integration of advanced technologies, like IoT, AI, and robotics, for enhanced manufacturing automation and industrial process connectivity.
Predictive analysis
Predictive analytics is an advanced form of data analytics that attempts to answer the question, “What might happen next?” As a branch of data science for business, the growth of predictive and augmented analytics coincides with that of big data systems, where larger, broader pools of data enable increased data mining activities to provide predictive insights. Advancements in big data machine learning have also helped expand predictive analytics capabilities.
Smart monitoring, often involving sensors and data analysis, allows for real-time tracking and proactive management of assets, systems, and processes, leading to improved efficiency, reduced costs, and better decision-making.
- Identifying Bottlenecks: Predictive analytics can help identify inefficiencies and bottlenecks in production processes, allowing manufacturers to optimize workflows and improve overall efficiency.
- Process Optimization: By analyzing data from the production process, manufacturers can identify areas for improvement and optimize processes to enhance product quality and consistency.
- Real-time Monitoring and Alerts: Predictive analytics can monitor production processes in real-time, identifying potential quality issues before they lead to defective products.


Industrial IoT
Industrial IoT (IIoT) solutions monitor, collect, exchange, and analyze real-time sensor data from your equipment. They can perform advanced analytics and deliver meaningful shop-floor insights.
AI and ML
AI and ML are transforming the manufacturing industry by enabling predictive maintenance, optimizing processes, improving quality control, and enhancing supply chain management, ultimately leading to increased efficiency, reduced costs, and improved product quality.
- AI and ML algorithms analyze data from sensors and maintenance logs to predict equipment failures and schedule maintenance proactively, minimizing downtime and repair costs.
- AI and ML can optimize production processes by identifying bottlenecks, optimizing resource allocation, and improving efficiency.
- AI-powered systems can detect defects in real-time using computer vision and machine learning, ensuring consistent product quality.
- AI and ML can optimize supply chain processes by forecasting demand, managing inventory, and improving logistics.
Digital Twins
A digital twin is a virtual representation of an object or system designed to reflect a physical object accurately. It spans the object’s lifecycle, is updated from real-time data and uses simulation, machine learning and reasoning to help make decisions.


Manufacturing Execution System (MES)
A Manufacturing Execution System (MES) is a software solution that monitors, tracks, documents, and controls the manufacturing process, bridging the gap between ERP systems and shop floor operations, providing real-time visibility and control for optimized production.
- Work Order Management: Tracks and manages production orders, ensuring efficient execution.
- Production Scheduling: Optimizes production schedules and resource allocation.
- Material Tracking & Traceability: Provides visibility into material usage and availability.
- Equipment Monitoring: Collects data from machines and equipment to monitor performance and identify potential issues.
- Quality Control: Supports quality control procedures and defect tracking.
- Downtime Analysis: Identifies and analyzes downtime events to improve efficiency.
Reporting & Analytics: Provides comprehensive reports and analytics on production performance.
Overall Equipment Effectiveness (OEE)
Overall Equipment Effectiveness (OEE) is a manufacturing metric that measures how efficiently a machine or process is performing, calculated by multiplying Availability, Performance, and Quality. It helps identify areas for improvement, track progress, and benchmark performance against industry standards.
OEE Factors:
- Availability: This factor considers unplanned and planned stops, with 100% meaning the process is always running during planned production time.
- Performance: This factor takes into account slow cycles and small stops, with 100% meaning the process is running as fast as possible when it’s running.
- Quality: This factor considers defects (including parts that need rework), with 100% meaning there are no defects (only good parts are being produced).
Benefits of Using OEE:
- Improved Productivity: By identifying and addressing losses, OEE can help improve overall productivity.
- Reduced Costs: Identifying and eliminating waste can lead to reduced costs in various areas, such as maintenance, scrap, and rework.
- Better Quality: Focusing on quality can lead to improved product quality and reduced customer complaints.
- Enhanced Decision-Making: OEE provides data-driven insights that can inform better decision-making regarding equipment maintenance, process improvements, and resource allocation.
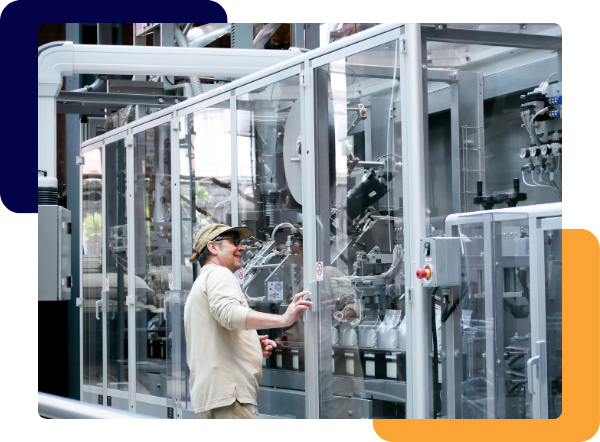